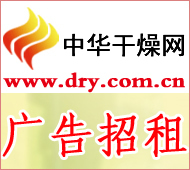
Zinc is an important strategic resource and an important basic material for the development of the national economy. China is a big country in terms of zinc resource reserves, production and consumption. However, sulfur dioxide and a large amount of iron-vanadium slag from zinc's traditional smelting methods have become a huge hidden danger of environmental pollution. To change this situation, it is imperative to open up new and more environmentally friendly zinc smelting methods. Recently, Wang Haibei, deputy director of the Metallurgical Research and Design Institute of the Beijing Research Institute of Mining and Metallurgy, one of the leaders of the “Eleventh Five-Year†National Science and Technology Support Program “Development of Sulphide Mine Clean Smelting Technologyâ€, stated that the traditional method was solved at the source. The problem of iron slag slag pollution and the goal of achieving clean production of zinc smelting have been achieved.
Sourcing into traditional smelters
Wang Haibei told reporters that at present, zinc smelting in China is based on traditional wet zinc smelting. After the sulphide ore is boiled and roasted, zinc is produced by “leaching-purification-electro depositionâ€, but zinc ferrite is produced during the roasting process, and the zinc content in the acid leaching slag is as high as about 20%. Although the sulfur dioxide produced by roasting is treated with acid, pollution is still inevitable.
According to the difference in acid leaching slag treatment process, the traditional process is divided into rotary kiln evaporation method and thermal acid leaching method. Rotary kiln treatment of acid leaching slag process will also release a certain amount of sulfur dioxide, and sulfur dioxide recovery of sulfuric acid produced by the storage and sale of sulfuric acid is limited by the transport radius, especially in remote areas and sulfuric acid surplus areas of sulfuric acid business is difficult to sell.
At the same time, the comprehensive energy consumption of rotary kiln volatile zinc smelting is relatively high. It takes 4 to 5 tons of high quality coke per ton of zinc metal produced. Although the energy consumption of zinc smelting by hot-acid leaching has been reduced, about 0.7 tons of iron-vanadium slag is produced per ton of zinc produced. The content of zinc is high and contains a large amount of heavy metal ions. So far, there is no more economical treatment method. Most enterprises use heap storage, which can easily cause environmental pollution.
Zinc recovery rate increased significantly
According to Wang Haibei's introduction, under the guidance of the principle of minimum chemical reaction volume, the lack of traditional techniques of the research group has proposed the use of pressure leaching technology for the first time to optimize the existing wet smelting process. The most important feature is that the iron vanadium removal process in the traditional zinc smelting method is eliminated, and the zinc in the solution is precipitated into the slag while zinc leaching is achieved. In this way, not only the process flow is simplified, but also the reaction is carried out under high temperature and high acid conditions, and the recovery rate of zinc is greatly increased. The problem of iron-vanadium slag contamination produced by the conventional method is solved at the source and the clean production of zinc smelting is realized.
During the research process, the research team of this project conducted a large number of experimental studies on the ratios of different schemes. While ensuring the zinc leaching rate, the amount of iron in the solution was reduced as much as possible. Through the optimization of the process, the recovery rate of zinc can be increased from 92.46% to 95.35%, and the iron content in the pressurized production solution can be reduced to less than 3 g/l, which reduces the difficulty of subsequent iron removal. Compared with the traditional hot-acid leaching-iron and iron removal process, the solids emission can be significantly reduced by 50%, and the zinc content in the slag is also less than 2%. The sulfur in the slag is recovered in the form of sulfur and the clean smelting is truly realized. produce. Zinc concentrate pressure leaching technology has the advantages of high recovery rate of zinc metal, small environmental pollution, and high comprehensive recovery rate, becoming an important direction for the development of zinc smelting. This technology realizes the direct leaching of sulphide ore, avoids the production of sulfur dioxide in the process, sulfur directly enters the slag in the form of sulfur, and can directly recover sulfur, thus solving the problems of sulfuric acid storage and sale.
New construction can be applied
Wang Haibei said that the technology is not only suitable for the construction of new plants, but also for the transformation of old plants. Compared with the traditional process flow, this process flow has minor changes. With a small increase in land occupation and investment, the metal recovery and production can be significantly increased. The output can be increased by 30% to 40%, and the production cost can be reduced by 2.68%. The economic benefits are very obvious. Under a relatively small investment risk, the company can effectively broaden the range of raw material processing and increase the overall metal recovery rate. More importantly, the technology has wide adaptability to raw materials and can achieve high-efficiency leaching of rare metals such as gallium and indium, which effectively improves the overall economic benefits of the company, and has great advantages in comprehensive recycling. In addition, the improvement of the processing and manufacturing level of domestic pressure leaching equipment has laid a foundation for the promotion and application of this technology.
Turbine Generator For Sale,Single Phase Dynamo,Magnet Generator For Sale,Generator Electric
Haiweineng Electrical Machinery Co., Ltd. , http://www.bgdieselgenerator.com