The ATEX directives, established by the European Committee for Standardization, focus on safeguarding individuals from explosive atmospheres within the European Union. These directives set out the fundamental safety requirements for both workspaces and equipment utilized in environments where explosions might occur. By addressing potential risks proactively, ATEX aims to create safer working conditions for employees across various industries.
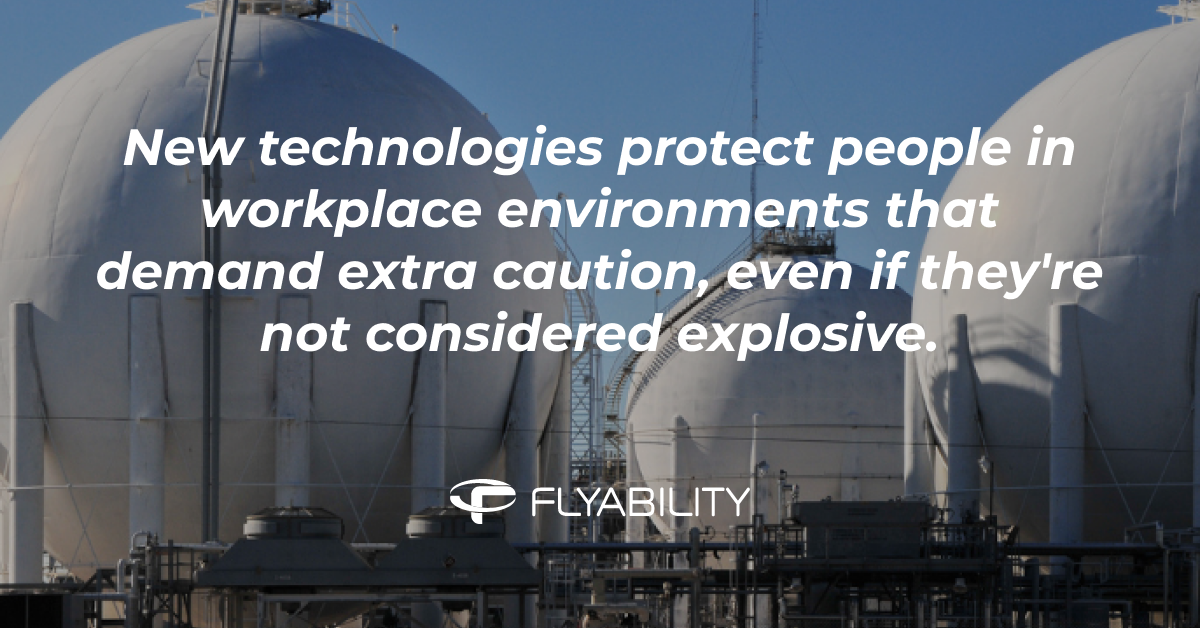
In particular, ATEX splits hazardous areas into distinct zones based on the likelihood of explosive atmospheres forming. This classification system helps determine appropriate safety measures and equipment specifications necessary for operations in these regions. For instance, zones related to gases and vapors are categorized as Zones 0, 1, and 2, each representing increasing levels of risk based on the frequency of explosive mixtures being present. Similarly, dust-related zones—Zones 20, 21, and 22—are defined similarly but pertain specifically to dusty environments.
Equipment used in these zones must also comply with specific categories depending on their intended application. Category 1 equipment is suitable for the highest-risk Zones 0 and 20, whereas Category 3 covers lower-risk Zones 2 and 22. Importantly, equipment certified for high-risk zones can also be employed in less hazardous ones, offering flexibility without compromising safety standards.
Beyond traditional methods of ensuring safety, modern advancements play a crucial role in protecting workers from dangerous conditions. Technologies like remote visual inspections via drones and robots enable access to hazardous areas without putting humans directly at risk. Although few robotic solutions fully meet ATEX’s intrinsic safety criteria, they remain invaluable tools for reducing exposure risks in industries dealing with explosive atmospheres.
Moreover, environmental mitigation strategies represent another effective approach to managing risks associated with explosive environments. By neutralizing the explosive properties of an area—often achieved through inerting techniques involving non-reactive gases—safe entry becomes possible even in otherwise perilous settings. Despite this reduction in immediate danger, personal protective gear remains essential during such interventions due to lingering risks.
As part of ongoing efforts to enhance worker protection, regular updates to ATEX directives reflect evolving best practices and technological innovations. Recent amendments introduced clearer definitions and updated terminologies while reinforcing the need for conspicuous warnings regarding potentially explosive zones. Such modifications underscore ATEX’s commitment to continuous improvement aimed at preserving occupational health and safety standards.
Ultimately, understanding and adhering to ATEX principles contribute significantly toward fostering safer industrial practices worldwide. Whether through stringent regulatory frameworks or innovative technological applications, prioritizing employee welfare continues to drive progress in minimizing workplace hazards linked to explosive atmospheres. As industries evolve, so too will the strategies employed to maintain optimal levels of security amidst challenging operational landscapes.
[For further insights into managing hazardous environments, consider exploring our latest resources on integrating advanced robotics into your safety protocols.]
Huai'an Senyu Intelligent Technology Co., LTD , https://www.jshasyzn.com