The ATEX directives are comprehensive safety regulations established by the European Committee for Standardization to safeguard individuals working in potentially explosive atmospheres within the European Union. These directives outline the fundamental safety criteria for both workspaces and equipment used in environments where explosive atmospheres might occur.
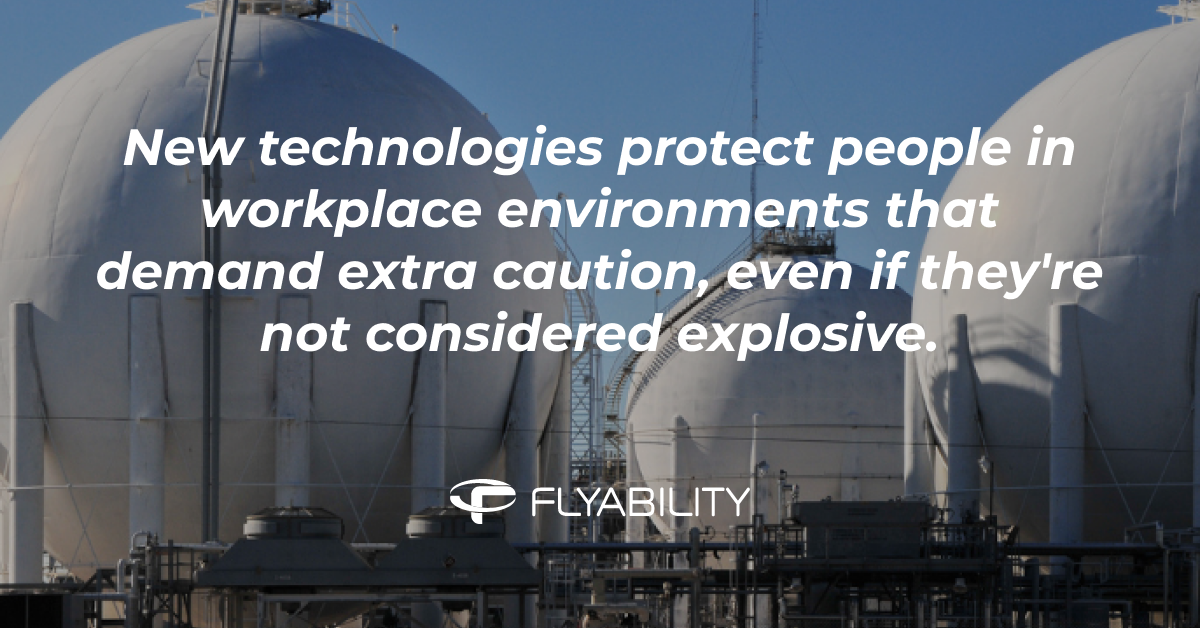
These directives are crucial because they ensure that workplaces and tools used in hazardous areas comply with strict safety standards. Industries such as oil, gas, and mining, where workers face challenging conditions, rely heavily on these regulations to classify potentially explosive zones into specific categories based on the likelihood of encountering an explosive atmosphere.
An explosive atmosphere arises when a mixture of air and flammable substances like gases, vapors, dust, or fibers has the potential to ignite upon contact with a spark. Efforts to create an international certification system akin to ATEX led to the development of the IECEx system, which offers a comparable approach to risk prevention. Although there isn't an identical ATEX equivalent in North America, several distinct yet similar frameworks exist, managed by various industry bodies.
Why is awareness of ATEX significant? It’s essential for everyone, especially professionals, to recognize the potential dangers inherent in industrial settings. Despite multiple layers of safety measures, complacency can lead to unforeseen incidents. Revisiting basic safety principles ensures that people remain vigilant about avoiding disasters, especially since preventable explosions continue to pose risks in industrial operations.
The ATEX zoning and categorization system divides hazardous locations into zones based on the frequency and duration of explosive atmospheres. Equipment used in these environments is also categorized according to the level of risk associated with each zone. For instance:
- **Gases/Vapors Zones**:
- **Zone 0**: Continuous presence of explosive gas mixtures.
- **Zone 1**: Explosive gas mixtures likely during normal operations.
- **Zone 2**: Rare occurrence of explosive gas mixtures.
- **Dust Zones**:
- **Zone 20**: Constant presence of combustible dust clouds.
- **Zone 21**: Occasional presence of combustible dust clouds.
- **Zone 22**: Rare occurrence of combustible dust clouds.
Equipment must adhere to specific categories corresponding to these zones, ensuring safe usage in different environments. Devices certified for higher-risk zones can also function in lower-risk areas, including non-hazardous locations.
ATEX contributes significantly to human safety by offering guidelines that minimize the risk of industrial explosions. Ensuring equipment, whether electrical or non-electrical, is intrinsically safe is paramount. This means the equipment’s design inherently prevents sparking under any circumstances. Tools like mobile tablets and personal safety alerts are examples of intrinsically safe devices used in hazardous areas.
Industries with explosive environments often involve tasks that require human intervention, particularly inspections to maintain overall safety. New technologies, however, are transforming how we approach these challenges. Remote visual inspections (RVI) conducted by drones and robots enable personnel to gather critical data without entering dangerous zones. While few robots meet ATEX’s intrinsic safety standards, they remain invaluable resources for industries dealing with hazardous environments.
Another approach involves environmental mitigation, where the atmosphere is rendered non-explosive by introducing inert gases like nitrogen. This allows controlled access for repairs or further inspections. Despite this, confined spaces still present significant risks, reinforcing the appeal of robotic solutions.
Advancements in technology not only enhance worker safety but also reduce costs and time spent on inspections. As a result, this method is gaining traction across various sectors.
Regular updates to the ATEX directives ensure compliance with evolving safety needs. The latest revision in 2014 introduced clarifications and terminology adjustments, along with clearer zone classifications and mandatory warning symbols for explosive areas.
In conclusion, the ATEX directives play a pivotal role in protecting workers in hazardous environments. By adhering to these standards, industries can mitigate risks effectively and promote safer workplaces.
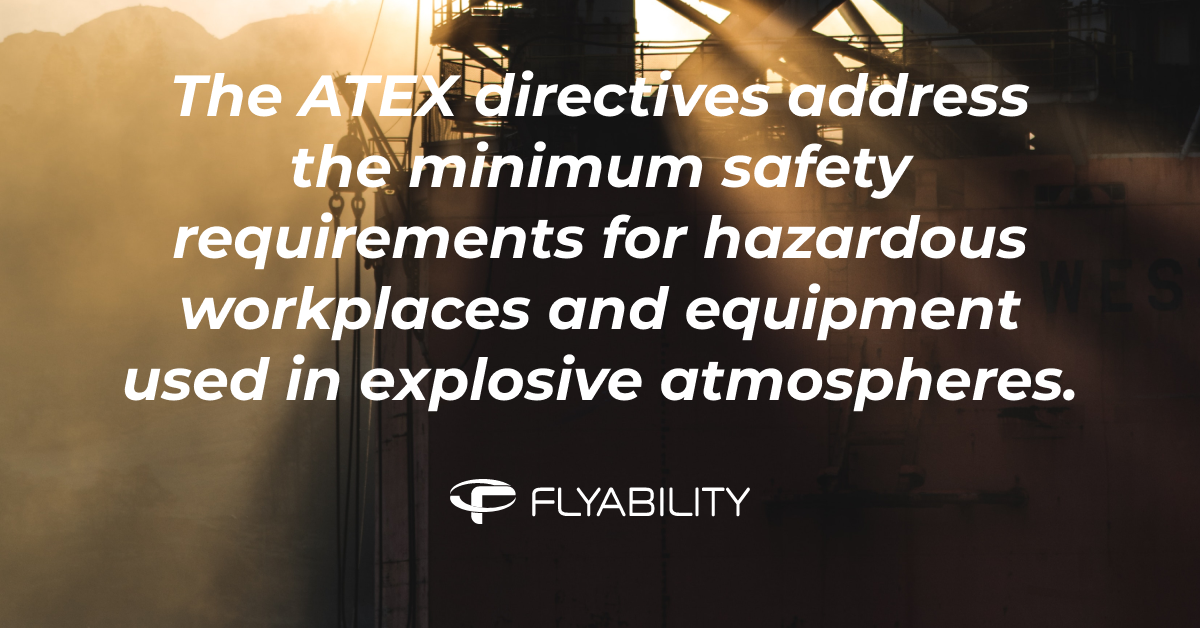
As technology continues to evolve, so too will our ability to safeguard workers, ensuring that the future of industrial operations remains secure and efficient.
Automotive Roll Forming Machine
Huai'an Senyu Intelligent Technology Co., LTD , https://www.jshasyzn.com