# The Elios 3 UT Payload: Redefining Safety and Efficiency in Hull Inspections
## Benefits At A Glance
| **Aspect** | **Description** |
|------------|-----------------|
| **Safety** | By deploying the Elios 3, there's no need for risky work at height, scaffolding, or entering confined spaces. This significantly reduces the hazards associated with ship hull or tank inspections. |
| **Speed** | The Elios 3 can be operational within just 30 minutes of arriving on-site. This cuts down thousands of hours previously spent setting up scaffolding. |
| **Localization** | The UT drone survey results are displayed within a 3D model, allowing easy identification and revisiting of points of interest for further analysis or maintenance. |
| **Reporting** | C-Bird successfully completed the UTM and close-up survey required for the ship’s 5-year periodic survey. Their data was certified by a leading class society. |
All shipping vessels are required to undergo special periodic inspections every five years, with smaller inspections scheduled more frequently. Older ships face more rigorous and regular inspections—major checks occur every 30 months for ships over 15 years old. These inspections are essential for ensuring the vessel meets safety standards and can continue operating. Critical to these inspections are ultrasonic thickness (UT) measurements to verify structural integrity, along with visual examinations of specific areas. Focus is placed on the midship section, which experiences maximum stress while at sea. Such inspections are crucial for detecting faults invisible to the naked eye or hidden within the ship's structure. Combining UT measurements with visual surveys ensures inspectors deliver accurate findings that comply with industry standards.
## Traditional UT Inspections on Ships
Traditionally, accessing UT inspection points and taking measurements often required significant manpower and time. Teams of up to 30 people would assemble scaffolding before a UT inspector could climb and measure. Erecting scaffolding poses inherent risks due to working at heights and introduces additional dangers to the ship—leftover pieces can damage pumps and necessitate drydock repairs.
This scaffolding setup for inspecting cargo tanks usually takes several days and demands special permits for working at height or in confined spaces. Additionally, the ship must be in drydock during the inspection, adding to the expense as drydock rates run between $4-6 million per day. Faster inspection methods, like using the Elios 3 UT drone, offer a cost-effective alternative without compromising on data quality.
Building scaffolding for surveying a 15-year-old tanker can cost between $300,000 and $700,000. Ships can remain out of commission for 40 to 60 days, with drydock fees reaching millions. Eliminating scaffolding not only improves safety but also drastically reduces costs.
C-Bird, a specialized ship inspection company, frequently employs the Elios 3 for UT inspections on vessels over 15 years old. They recognize that the Elios 3 offers faster results than conventional methods while capturing the necessary UT and visual data. This enhances safety standards and slashes scaffolding management costs, expediting the entire process.
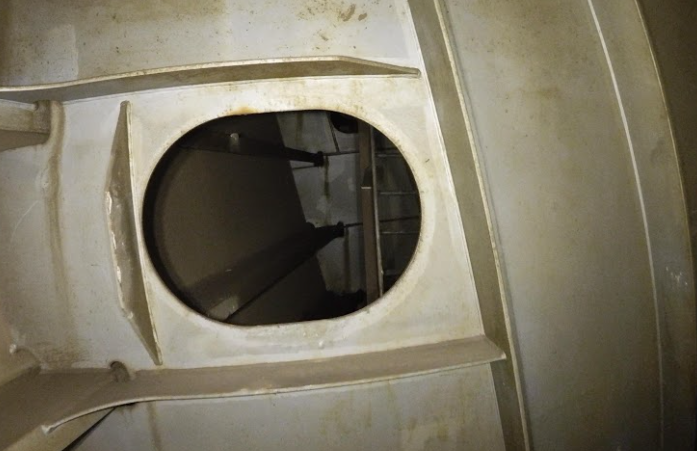
*Image: Scaffolding involves extensive labor and carries significant risks, especially at height.*
## How UT Drone Inspections Benefit The Maritime Industry
C-Bird was tasked with inspecting 12 oil tanks in a medium-sized ship. CEO Malcolm Connolly was asked to perform gauging measurements and close-up inspections of the oil tanks as part of the ship’s periodic survey. Each tank measures 38 x 28 x 20 meters, with six transverse web frames in each cargo oil tank (COT) and transverse bulkheads separating each COT.
For this project, Malcolm and the C-Bird team utilized the Elios 3 and its new UT payload. The drone excels at detailed LiDAR mapping and visual inspections. Visual inspections are essential for periodic surveys since any records must be captured at arm’s length from the inspected object. The drone swiftly gathers this visual data at the required distance without requiring inspectors to climb scaffolding or enter confined spaces. As a Flyability product advisor and beta-tester for the new UT payload, Malcolm viewed this as an ideal opportunity to test the drone’s performance alongside the ship’s visual inspection.
## Conducting A Ship UT Inspection With The Elios 3
Rather than relying on traditional labor-intensive methods, C-Bird employed the UT probe with two Elios drones to inspect the 12 oil tanks. They conducted the inspections under the guidance of a class inspector who specified the testing requirements. This drone-based inspection method was far quicker than the usual scaffolding approach—once onboard, the UT inspection could start immediately, saving time compared to the thousands of hours associated with scaffolding. C-Bird navigated the Elios 3 UT drone around each tank and took measurements in multiple locations as per the inspection plan and any extra areas requested by the class surveyor. Both UT and visual inspections were completed within seven days. Afterward, the pilots confirmed with the class inspector that the Elios 3’s spot measurements matched the required number and location.
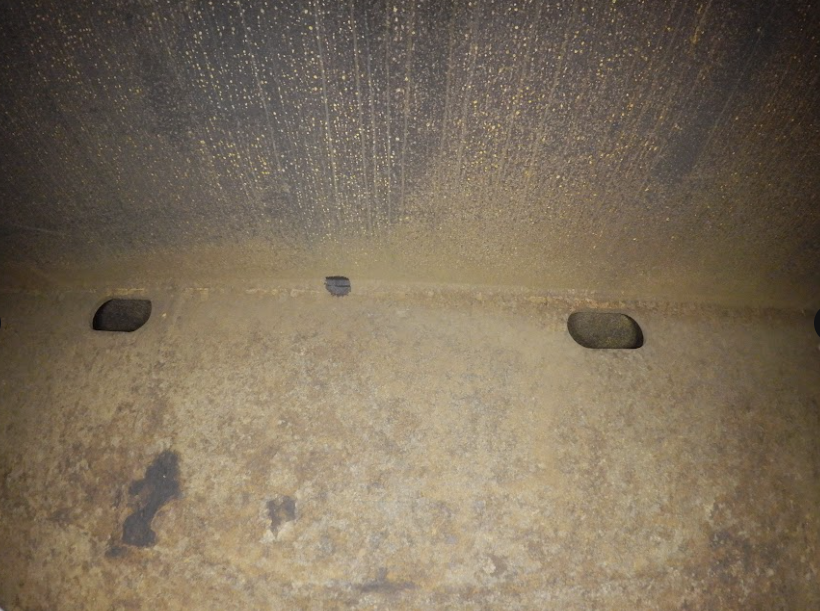
*Photo: Close visual inspection with the Elios 3 inside the COTS.*
The Elios 3 streamlined the visual inspections required for this process. The drone allowed pilots to collect both visual and UT data during the flights, offering a close-up view of the surveyed areas at the required distance. This enabled C-Bird to gather the necessary information twice as fast, with one drone focusing on visual inspections and the other on UT measurements. The results included a clear visual display of points of interest along with UT spot measurements.
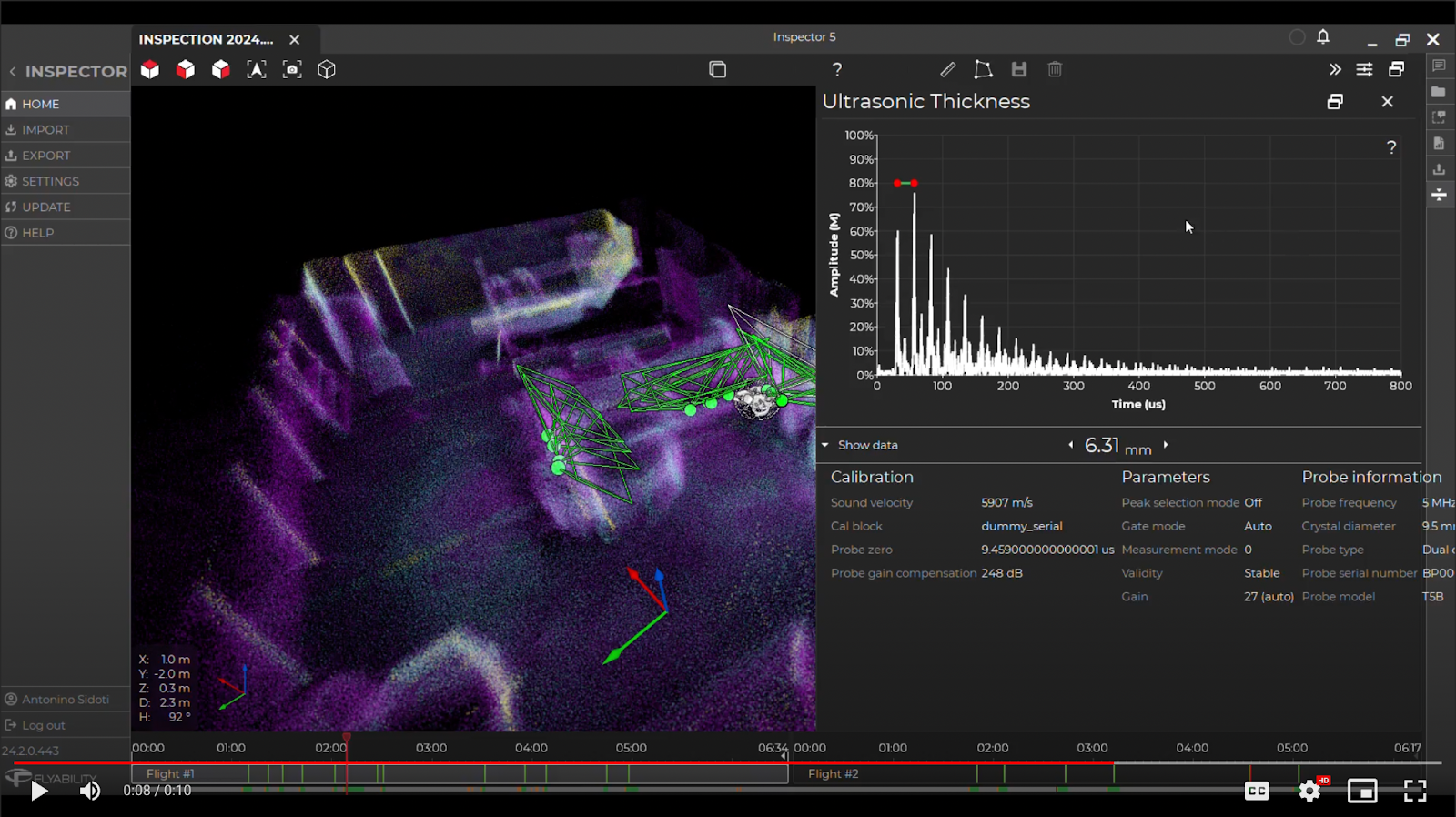
*Example point cloud with Elios 3 UT payload showing spot measurements.*
The C-Bird team organized the collected data into the format required by the class society and submitted the inspection for review. This was significantly faster than traditional methods since all data collection occurred in one session, eliminating the need to adjust scaffolding or MEWP platforms.
## Certified Results From Using The Elios 3 For A UT Ship Inspection
After two years of successful pilot projects, C-Bird and their Elios 3 UT payload results received certification from the American Bureau of Shipping, one of the major class societies worldwide, as an approved recognized service provider for ESP hull gauging (Enhanced Survey Program). This marked the first time such recognition was granted, highlighting C-Bird’s achievements with drone inspections.

*Watch the Elios 3 utilize its live 3D model to guide the drone and make a UT measurement, marking it as a point of interest for reporting.*
The Elios 3 delivered five key advantages for C-Bird. First, the team could easily locate UT spot measurements within a clear point cloud. Second, the inspector could access the entire space more safely than with scaffolding or other methods while minimizing risk exposure. Third, the drone provided reliable results certified by the class inspector. Fourth, the Elios 3’s versatility allows it to serve as a comprehensive inspection tool adaptable to various environments with relevant payloads. Lastly, C-Bird could deliver detailed reports matching the class society’s required format, proving the drone’s value not only as a UT inspection tool but as an asset for multiple ship inspections.
C-Bird plans to continue using the Elios 3 and its UT payload for visual and ultrasonic thickness inspections across multiple industries, including maritime, oil and gas, and asset management. The comprehensive results achieved with the drone set them apart from competitors and traditional methods through enhanced speed, safety, and data quality. This approach has opened a new era for confined space and challenging UT inspections—C-Bird eagerly anticipates deploying the Elios 3 in new and exciting projects.
Discover more about the Elios 3 and its UT payload today!
---
*Note: This article reflects real-time insights based on ongoing developments in drone technology and its applications.*
Fixed Tube Heat Exchanger
Fixed tube heat exchanger consists of tube bundle, tube plate, shell, head, folded plate, etc. Tube bundle ends fixed in the tube plate, the tube can be expanded (the inner hole of the tube with mechanical expansion, so that the tube wall from the inward to outward extrusion and fixed in the tube plate) or welded to the tube plate. The tube bundle is placed within the tube shell, with headers and flanges fixed at both ends. In this way, one fluid flows from the inside of the tube and the other from the outside. The space between the two heads and the tube plate is used to distribute or collect the fluids inside the tube. The two fluids do not mix with each other, but only exchange heat through the tube wall.
Advantages: simple and compact structure, high pressure resistance, low cost and easy to clean the tube side.
Disadvantages: Risk of blockage when the tube is damaged or needs to be replaced.
When the difference between the wall temperature of the tube bundle and the shell or the coefficient of linear expansion of the material is large, a large thermal stress will be generated in the shell and the tube bundle. A flexible compensation ring (also called expansion joint) should be installed on the shell to reduce the thermal stress.
Fixed Tube Heat Exchanger,Tubular Exchanger,Tema Heat Exchanger,Fixed Tube Sheet Heat Exchanger
Guangdong Jiema Energy Saving Technology Co.,Ltd , https://www.jmheatexchanger.com