The domestic second-hand dryer can be divided into two types: boiling granulation second-hand dryer, centrifugal spray second-hand dryer, vacuum freezing second-hand dryer, and so on. On the whole, the development of second-hand dryers in China is relatively rapid, but when the second-hand dryers in China have reached a stage of rapid development, second-hand dryers in China have encountered a major bottleneck in their development.
Compared with developed countries, there are still some gaps in the quality and technical level of domestic used dryers. The lack of theoretical research is a major bottleneck restricting the development of secondary dryers in China. The physical properties of the materials to be dried are varied, and only a few drying equipments cannot meet the needs of production.
Theoretical research is the basis for the development of new dryers. With the development of drying technology in China, it is necessary to cultivate a group of theoretical research and drying technology development workers to improve the technical content of drying equipment in China.
In recent years, although some colleges and universities or scientific research units in China are doing this work, the input of human and material resources is far from enough. In terms of theoretical research, there is still a big gap between China and Denmark, Canada, Japan and other countries.
The lack of technology is the second bottleneck that restricts the development of second-hand dryers in China. The low automation level of domestically-made second-hand dryers and the lag in control means are common problems. In recent years, with the increasing emphasis on the industry and the intensity of investment, the current status of secondary dryers in China is moving toward better and better directions and goals.
Gamma Laser Cutting Cabinet Nitrogen Generator is installed into one cabinet, it has compact structure, no need for site installation, plug and play, one simple push on starting button, Nitrogen Generator begin to work. Its purity can be 99.995-99.9995%, 45 Nm3/hr flow rate, 30 bars outlet pressure. For smaller laser cutting machine, there is also smaller nitrogen generator with 15 Nm3/hr flow rate.
The principle of laser cutting is performed by a high-energy laser beam melt metal material, high pressure and high flow gas is used to blow the melted metal material, forming cutting slits. NC system controls the motion axes to complete graphics processing.
In laser cutting operating, the cost of N2 (nitrogen) gas has reached 1/3-1/2 of total cost. To reduce laser cutting machine customers` nitrogen gas consumption cost, Gamma developed nitrogen generator exclusively for laser cutting application. With this nitrogen generator, customers not only can get low cost nitrogen gas, but also increase the utilization ratio of nitrogen, reduce the consumption of oxygen.
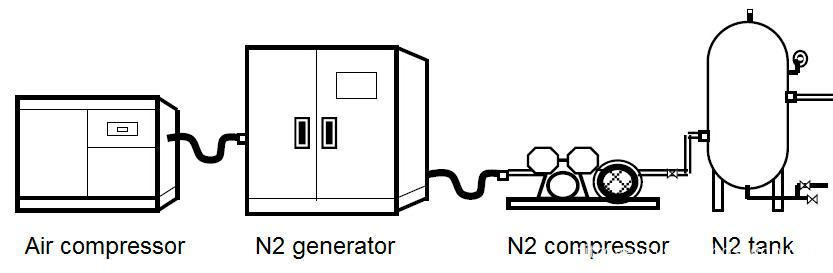
Laser Cutting Nitrogen Generator
Laser Cutting Nitrogen Generator,N2 Generator For Laser Cutting,Nitrogen Generator For Laser Cutting,PSA Nitrogen Generators,Nitrogen Generators Ce,Onsite Nitrogen Generators,Cylinder Filling Nitrogen Generators
Shandong Gamma Gas Engineering Co. Ltd. , https://www.gammagas.com