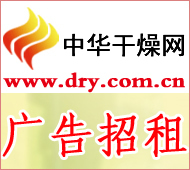
It is the traditional direction of the development of the chemical industry that large-scale equipment of China Drying Network Co., Ltd., but it is also accompanied by increasingly prominent problems of efficiency, safety and environment while gaining economies of scale. Contrary to this, the micro-miniaturization of equipment can improve the space-time efficiency when the equipment volume is greatly reduced, and the large-scale industrial production and chemical process can be safely controlled. It is considered as a major breakthrough in the concept of modern industrial development. . The micro-structured chemical mass transfer equipment and industrial application projects completed by Prof. Luo Guangsheng and Prof. Lü Yangcheng of Tsinghua University have overcome the worldwide difficulties in the industrialization of micro-structured chemical equipment and realized the micro (small) type of chemical equipment from concept to concept. The leap in industrial practice has reached the international leading level as a whole, and thus won the second prize of the National Science and Technology Award for Technological Invention.
Micro-chemical technology is the cutting-edge technology that emerged in the early 1990s. It is based on micro-scale multiphase flow, transfer and reaction, which creates the conditions for a more efficient and safe material transformation process. For example, the current industrial application of hydrocarbon nitration time is generally tens of minutes to several hours, while the use of micro-chemical technology, the reaction time can be shortened to several seconds. The key to the industrialization of micro-chemical technology is to create micro-structured chemical equipment. The key scientific issue is the mechanism and method for the large-scale preparation of micro-scale air bubbles/droplets for complex industrial systems. The United States, Germany, Japan and other chemical-intensive countries have started research on micro-structured chemical equipment since the 1990s, but it has rarely been reported in large-scale chemical production.
After many years of research, the project team has made major breakthroughs in the large-scale preparation of micro-scale bubble/droplet groups, the selection of materials and structural optimization of micro-structured equipment, and the reliability of applications for complex systems. It has successively developed membrane dispersion equipment. , micro-screening equipment and co-current micro-grooves equipment, and for the first time successfully applied to large-scale chemical production. Prof. Luo Guangsheng said that compared with traditional chemical equipment, micro-structured equipment has the advantages of high mass transfer efficiency, small amplification effect, and safety and controllability. It can significantly increase the utilization efficiency of resources and energy in the reaction process, and its popularization and application will help The chemical industry is advancing towards efficiency, greenness and security, and it has tremendous economic and social benefits.
For the large-scale application of gas-liquid, liquid-liquid mass transfer processes, and the problem of high processing volume and high cost of fine structures, the project team developed a multi-channel membrane dispersion equipment, and pioneered the breakthrough in micro-structure equipment in the international community. Scale application of technical problems. Prof. Luo Guangsheng introduced that the preparation of nano-calcium carbonate using Ca(OH)2 slurry to absorb CO2 is a typical process. The project team invented membrane dispersion to prepare nano-calcium carbonate technology. This process requires not only that the mass transfer between the gas and liquid phases be completed in milliseconds to increase the supersaturation and reduce the particle size, but also that the gas-liquid mixing in the reactor is required to make the particle size distribution of the nanoparticles narrow. Conventional equipment carbonization towers, stirred reactors, etc. cannot meet these requirements.
Membrane dispersion equipment controls the contact scale of gas-liquid two-phase to micron level, and the time for completing the mass transfer between phases is less than 100ms. The thin layer shear dispersion ensures that the gas-liquid mixture is even, and thus the particle diameter can be within the range of 10 to 70 nm. Large-scale preparation of nano-calcium carbonate with a narrow particle size distribution. The first international set of Ca(OH)2 slurries to absorb CO2 to produce nano-calcium carbonate industrial micro-structured equipment, a single processing capacity of 200m3 / h, residence time <100ms, volumetric mass transfer coefficient than tower, tube and other conventional equipment 1 to 2 orders of magnitude higher. Industrial production shows that the new technology has outstanding advantages such as controllable product quality, high CO2 utilization, low energy consumption, and small amplification effects.
The complexity of chemical systems and processes has brought many challenges to the material selection and structural parameter design of micro-structured equipment. For example, the wet-process phosphoric acid extraction and purification system involves inorganic acids, organic solvents, metal ions and other substances, requiring the use of special equipment materials; the process involves extraction, washing and stripping, requiring equipment in the range of 3 to 20 Has a very good mass transfer performance.
In response to the above-mentioned process conditions and high material requirements, the project team innovated the design method and successfully developed a micro-sieve hole device with a single P2O5 capacity of 5kt/a with corrosion-resistant materials as the main body and it has been continuously and stably operated. It can well adapt to the strong corrosive wet-process phosphoric acid system and can completely replace the imported equipment, breaking the monopoly of Bateman and other foreign companies in this field. Compared with the imported equipment, the size of the equipment is reduced to 1/2000, the manufacturing cost is 1/50, and the driving time is reduced from 5 to 7 days to 2 to 4 minutes. In the range of 3 to 20, the mass transfer efficiency can reach more than 95%, reflecting the good designability of micro-meshing equipment.
In addition, for many complex systems such as systems containing solid slag, high interfacial tension, and large differences in the physical properties of the two phases, it is difficult to obtain micron-sized droplets using submicron-sized microsieve pores only by shearing, and the solid slag may block the microparticles. Sieve, it is difficult to achieve efficient mass transfer and stable operation of equipment. The project team proposed a fluid pre-dispersion scheme and developed a stack-type parallel-flow micro-tank device with large flux, easy processing, and high efficiency. It is not easy to foul and plug when processing solids-containing systems. It was already 160 kt in November 2008. Industrial applications have been achieved during the extraction of the /a caprolactam acid group. This is the first industrial application of an industrialized microextractor on a global scale.
Compared with the devices imported from Italy, the mass transfer efficiency has been increased from 85% to more than 98%, and at the same recovery rate, the amount of extractant can be reduced by 30%. Under the same operating conditions, the intermediate cyclohexane can be reduced. Loss of 50% alkane carboxylic acid, with its phase separation equipment can increase the processing capacity of 50%.
Electric Valve,Pulse Valve,Electric Solenoid Valve
Century New Power International Trade Co., Ltd. , http://www.tjdustcollector.com